The Lost Wax Technique: Crafting Timeless Fine Jewelry
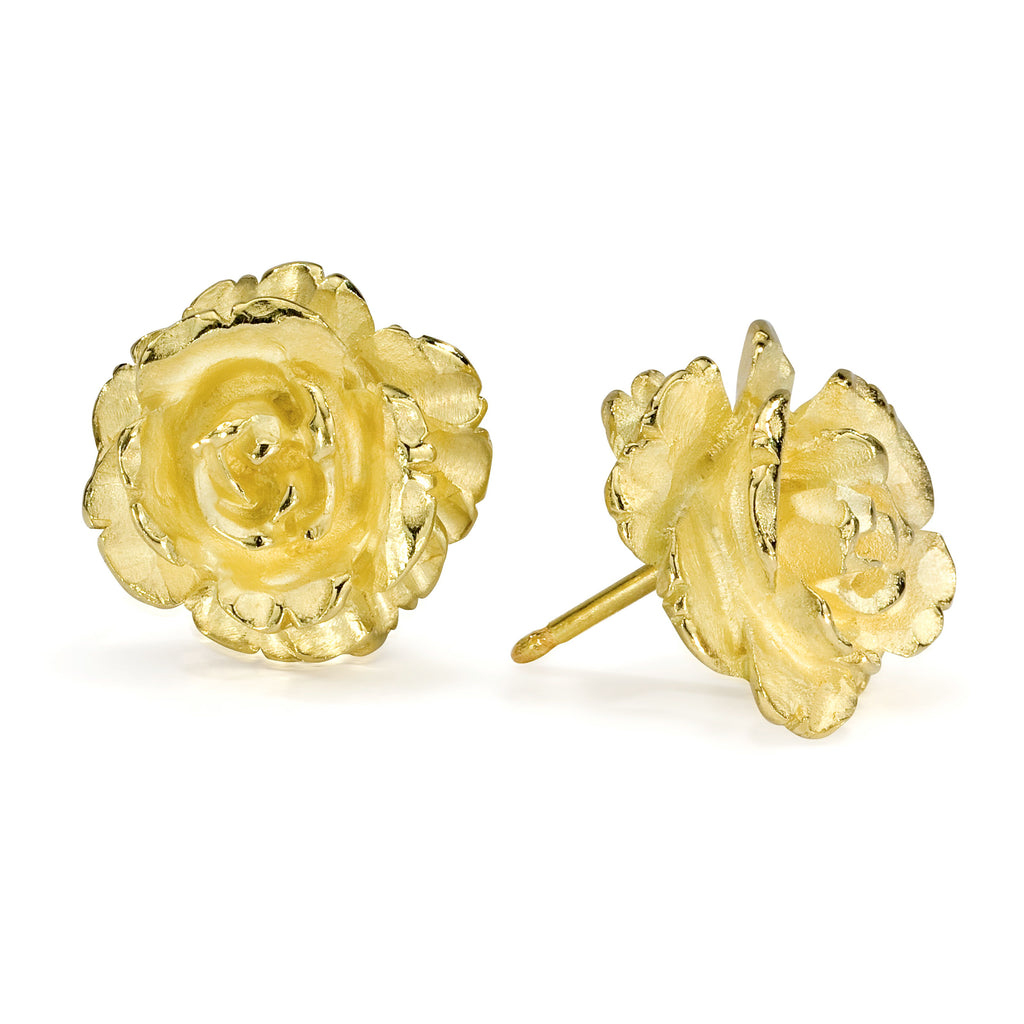
The Lost Wax Technique in Fine Jewelry Making: A Timeless Craftsmanship
When it comes to creating fine jewelry, there is a technique that has stood the test of time, revered for its ability to transform vision into reality with unmatched precision and artistry: the lost wax technique. Known as “cire perdue” in French, this ancient method dates back thousands of years and continues to be a cornerstone of jewelry craftsmanship. At Via Orefici, we honor this tradition by using the lost wax technique to bring some of our designs to life.
A Brief History. The lost wax technique is believed to have originated in ancient civilizations such as Mesopotamia, Egypt, and the Indus Valley around 5,000 years ago. This method was used not only for jewelry but also for crafting intricate sculptures, statues, and other decorative objects. Over centuries, the technique spread across cultures and continents, evolving and refining into the sophisticated process we know today. Despite the advent of modern technology, the lost wax technique remains highly valued in the world of fine jewelry for its ability to produce intricate details.
How the Lost Wax Technique Works. The lost wax technique is a multi-step process that involves creating a detailed wax model of the desired jewelry piece. Here’s a simplified breakdown of how this fascinating method unfolds:
Design and Wax Modeling: The process begins with a concept or sketch, which is then translated into a three-dimensional wax model. This model, carefully crafted by hand, is the replica of the final piece of jewelry, complete with all the delicate details that will later be captured in metal.
Molding and Investment: The wax model is then attached to a wax “tree” and placed inside a metal flask. The flask is filled with a plaster-like substance called investment, which encases the wax model. Once the investment hardens, it forms a mold around the wax.
Wax Burnout: The flask is heated, causing the wax to melt and burn away, leaving a hollow mold in its place. This step is where the technique gets its name—since the wax is “lost” during the process.
Casting: Molten metal, such as 18-karat gold or sterling silver, is poured into the hollow mold through a carefully designed channel system. The metal fills the space left by the wax, capturing every tiny detail of the original model.
Revealing the Masterpiece: After the metal cools and solidifies, the investment mold is broken away to reveal the raw jewelry pieces. The pieces are then cleaned, polished, and finished by skilled artisans who may add gemstones, engravings, or other final touches and other gold's details to complete the work.
Why the Lost Wax Technique Matters in Fine Jewelry. The lost wax technique is cherished because, unlike mass-produced jewelry, each piece created using this method is truly unique, bearing the subtle nuances of the artisan’s hand. This technique allows for exceptional detail and complexity, making it ideal for custom jewelry or designs that require delicate patterns, textures, or organic forms. The artisans work closely with each design, ensuring that the final piece captures the essence of the original vision while showcasing the beauty of the materials. This hands-on approach not only preserves the artistry of jewelry making but also connects each piece to a legacy of craftsmanship that spans centuries.
A timeless tradition and a reminder that, even in a world of rapid technological advancements, some methods remain irreplaceable. At Via Orefici, we are proud to continue this tradition, creating jewelry that tells a story of dedication, skill, and artistic heritage.
Leave a comment